CAPABILITIES
Rubber molds: Custom solutions for complex needs
At DTM, we specialize in designing and manufacturing high-quality rubber molds tailored to meet the unique demands of various industries, particularly the automotive sector. Our expertise ranges from quick prototypes to complex multi-cavity automated production molds, ensuring we an handle even the most challenging projects with precision and efficiency.
Rubber Molds
Molds
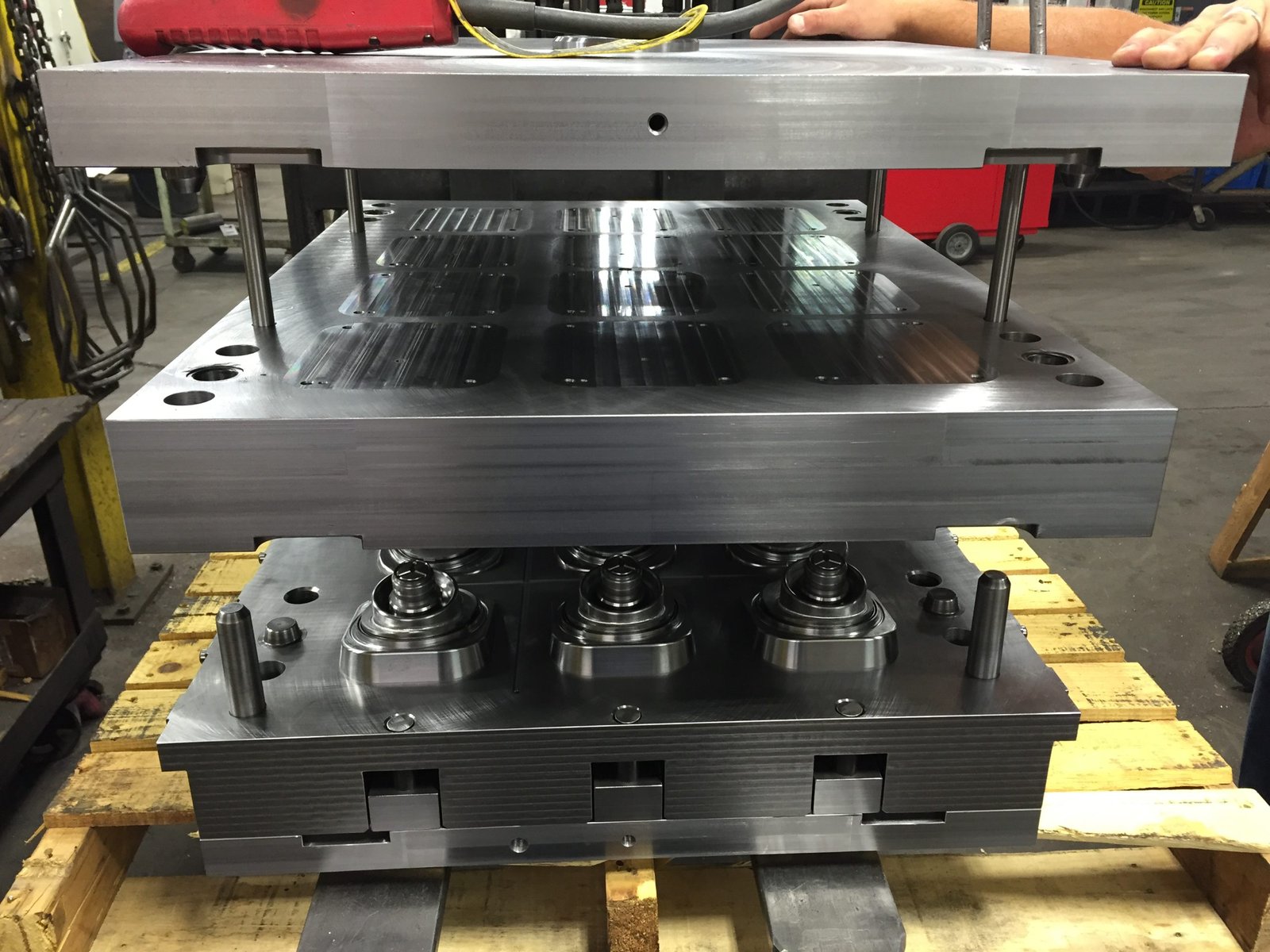

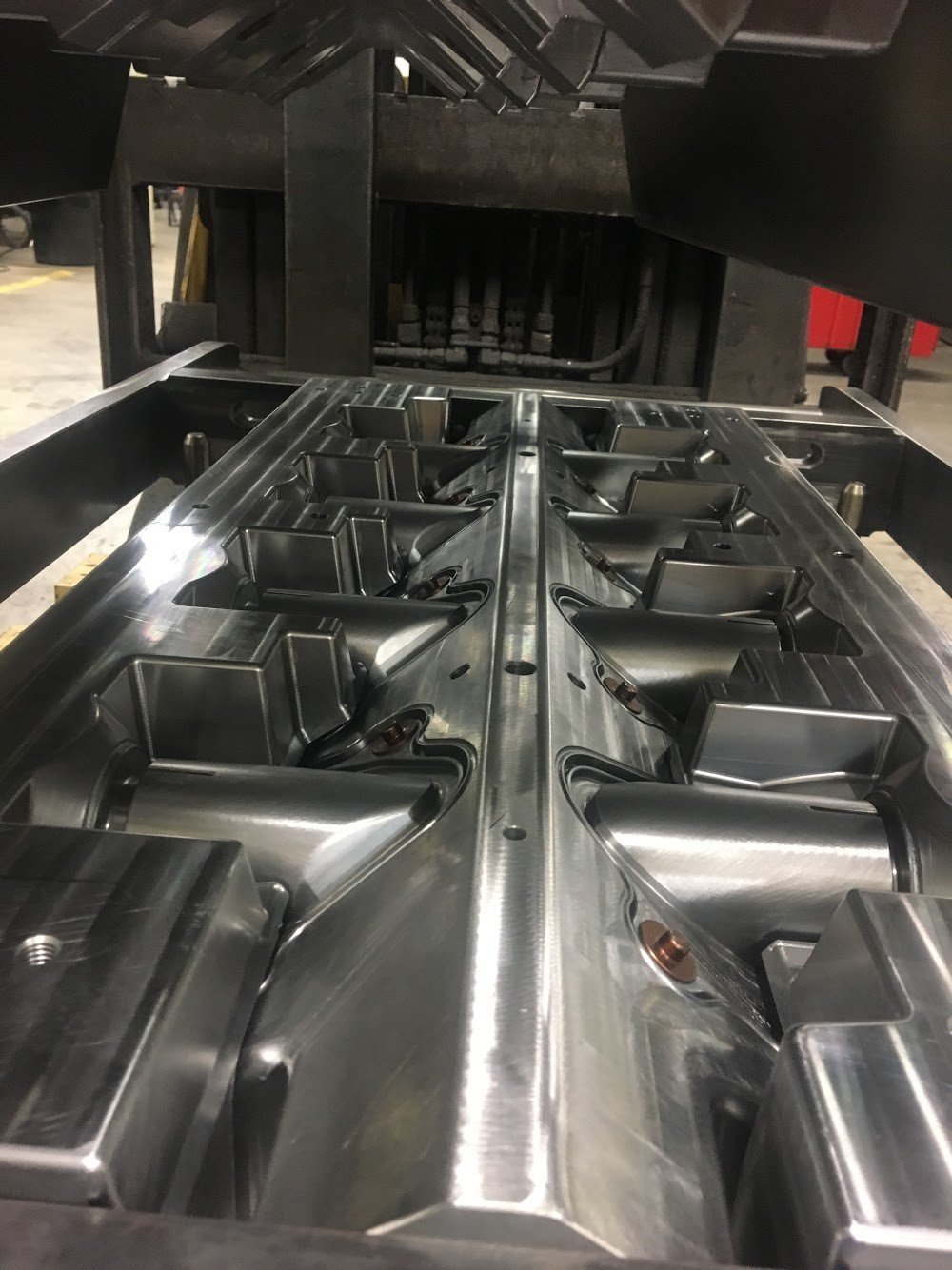


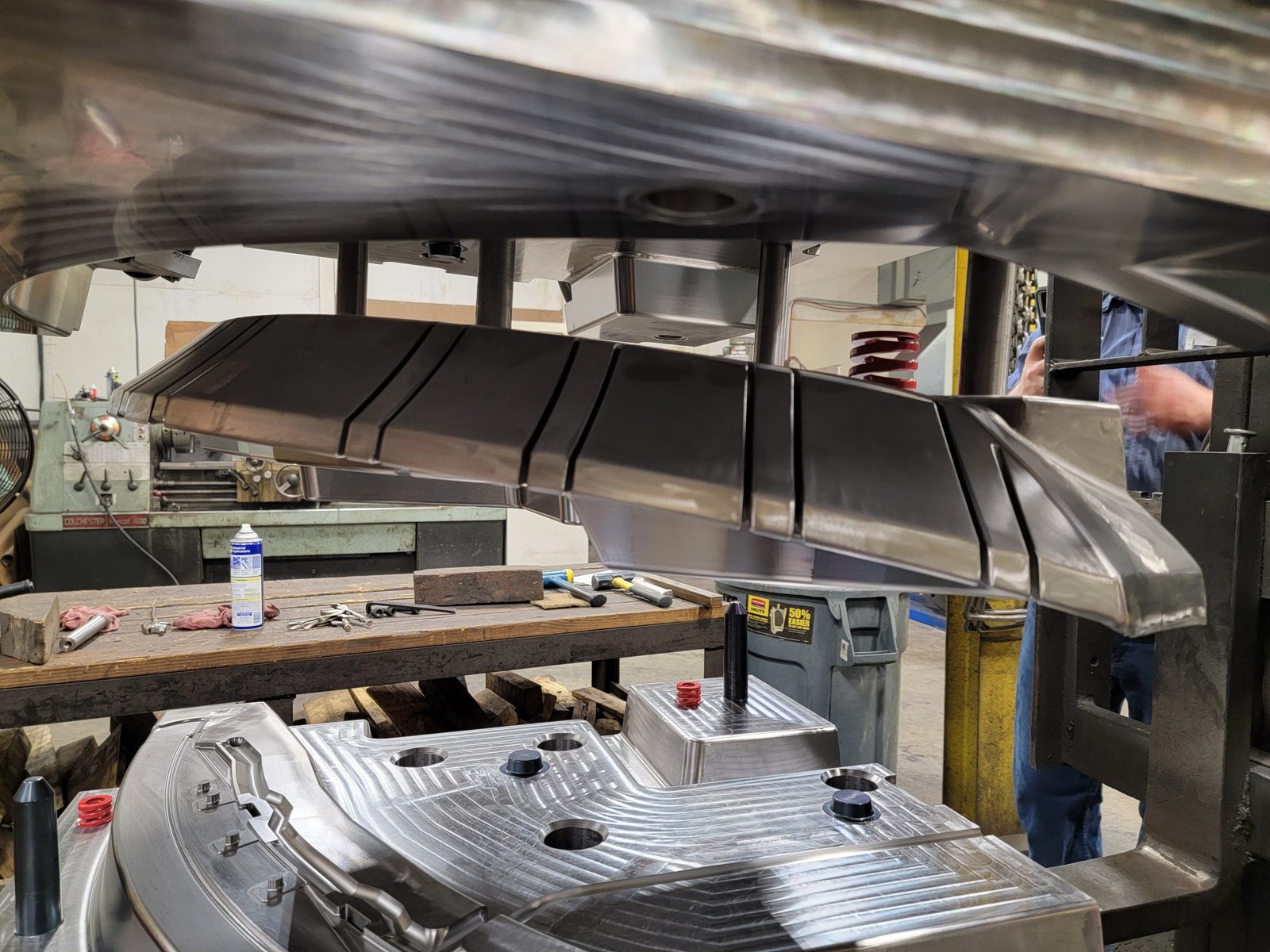

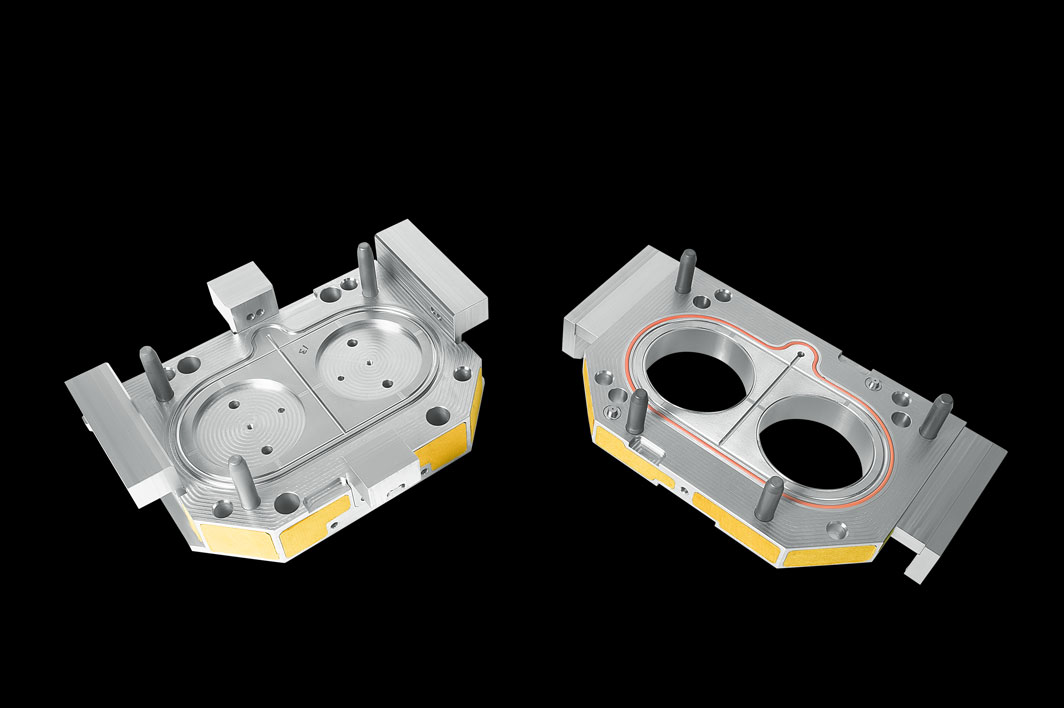
Comprehensive rubber mold capabilities
DTM offers a wide variety of rubber molds, each tailored to specific applications and industries. Our capabilities include:
Compression molds
For durable, high-volume parts across various materials.
Injection molds
Top/side injection with hot/cold runners for efficient material flow.
Transfer molds
Low-waste and conventional designs for complex geometries.
Metal to rubber bonding
Strong, durable bonds for demanding applications.
Rotary tooling
High-efficiency production tools.
3D complex cavities
Precision molds for intricate designs.
Precision molds for intricate designs.
Enhanced mold functionality.
Popup cores, stripper plates
Streamlining automated processes.
Sliding/split bars
For complex mold designs.
Automation
Advanced systems for streamlined production.
Repair and reverse engineering
Extending mold life and functionality.
Demolding systems
Efficient part removal solutions (KO tables, etc.).
From rubber injection molding and compression molding to transfer molding and rubber-to-metal bonding, DTM has mold-making capabilities to meet your needs.
These capabilities allow us to meet diverse customer needs with customized, high-quality solutions.
The DTM process: Confidence from concept to completion
At DTM, our process is thorough and efficient, ensuring that every part we produce meets the highest standards of quality and durability. Here’s how we approach each machining project:
Engineering and design
Each project starts in the engineering and design phase. Whether you’re working from a completed design or just have a simple sketch, we ensure that your precision parts or tooling components are thoughtfully engineered to meet your needs and budget.
Our skilled engineers use the latest CAD/CAM software to create detailed designs and programming for simple to complex multi-axis parts. Our quality control process starts at the design phase, ensuring components are engineered to the highest standards, and saving you money over the life of the project.
1. Initial consultation
We start by discussing your part design, project requirements, and molding press specifics. This allows us to provide you with an accurate quote and timeline, typically within 2 days to 2 weeks, depending on project size.
2.Design review and collaboration
After agreeing on a design, our team creates a rough draft for your review. This collaborative step ensures that our visions are aligned before we move forward.
3. Final design approval
Once the design is finalized and approved by you, we begin the manufacturing process. Our designer, project manager, and engineers work together to review every detail, ensuring that your tooling is built to last.
4. Component manufacturing
We strategically machine certain parts during this stage to ensure a perfect fit within the molds. This attention to detail guarantees that your tooling will have the best quality and longevity possible.
5. Assembly and testing
As we assemble the tool, we can still make adjustments to ensure optimal fit and function. Once completed, we test the tool to confirm that it works correctly before approving it for shipment.
6. On-time delivery
With DTM, you can trust that your rubber molds will be delivered on time, defect-free, and ready for use in your press. We also have the capabilities to do quick-turn work for urgent needs.
Addressing potential issues upfront
The further you get in the mold-making process, the more costly changes become. At DTM, we address all potential molding defects during the engineering and design stages.
Our team carefully examines your part design to identify and mitigate issues such as knit lines, sink, contamination, delamination, and more. This proactive approach not only saves time and money but also ensures that your molds produce high-quality, consistent parts from the start.
Materials and presses we work with
Engineering and design
Each project starts in the engineering and design phase. Whether you’re working from a completed design or just have a simple sketch, we ensure that your precision parts or tooling components are thoughtfully engineered to meet your needs and budget.
Our skilled engineers use the latest CAD/CAM software to create detailed designs and programming for simple to complex multi-axis parts. Our quality control process starts at the design phase, ensuring components are engineered to the highest standards, and saving you money over the life of the project.
We are experienced in working with a wide range of material types, including:
- EPDM
- NR
- Butyl
- Peroxide cured
- Viton
- Silicon
Engineering and design
Each project starts in the engineering and design phase. Whether you’re working from a completed design or just have a simple sketch, we ensure that your precision parts or tooling components are thoughtfully engineered to meet your needs and budget.
Our skilled engineers use the latest CAD/CAM software to create detailed designs and programming for simple to complex multi-axis parts. Our quality control process starts at the design phase, ensuring components are engineered to the highest standards, and saving you money over the life of the project.
We manufacture rubber molds for a range of press types, including:
- Desma
- Maplin
- Republic
- US Molding
These capabilities enable us to deliver versatile and reliable rubber molds that meet the highest industry standards.
Custom machining solutions for automotive rubber molds
The automotive industry is one of our primary focus areas, and we have a proven track record of delivering high-quality rubber molds for various automotive applications.
From fender flairs to air induction boots and steering column boots, our molds are designed to meet the rigorous demands of the automotive sector.
Why choose DTM as your rubber mold manufacturer?
At DTM, we are dedicated to providing our clients with the highest level of service and quality. Here’s what sets us apart:
Engineering and design
Each project starts in the engineering and design phase. Whether you’re working from a completed design or just have a simple sketch, we ensure that your precision parts or tooling components are thoughtfully engineered to meet your needs and budget.
Our skilled engineers use the latest CAD/CAM software to create detailed designs and programming for simple to complex multi-axis parts. Our quality control process starts at the design phase, ensuring components are engineered to the highest standards, and saving you money over the life of the project.
Experience
Confidence
We are confident in our capabilities so that you can be, too. Have a tough molding challenge? We get creative to deliver the solutions you need.
Precision
Our commitment to precision ensures that every mold we produce meets the highest standards of quality and durability.
Customer focus
We partner with you to ensure your needs are met at every stage of the project, from design to delivery. We pride ourselves on clear communication so you’ll know where your project stands at all times.
Innovation
We continuously invest in the latest technology, techniques, and training to provide cutting-edge solutions that drive your success.