Repair/Replacement Services
Tool and die repair and replacement services
Restoring functionality and extending the life of your equipment
As your expert tool and die maker, DTM doesn’t just specialize in manufacturing; we also provide the highest-quality tool and die repair and replacement services to keep your equipment running smoothly and efficiently.
Our expertise in repairing and replacing worn or damaged parts, molds, and automation equipment means you can minimize downtime and maximize productivity. Whether you’re dealing with outdated tools, compromised die parts, or difficult-to-find components, DTM has the knowledge and experience to reverse engineer and manufacture the parts you need to get back on track.
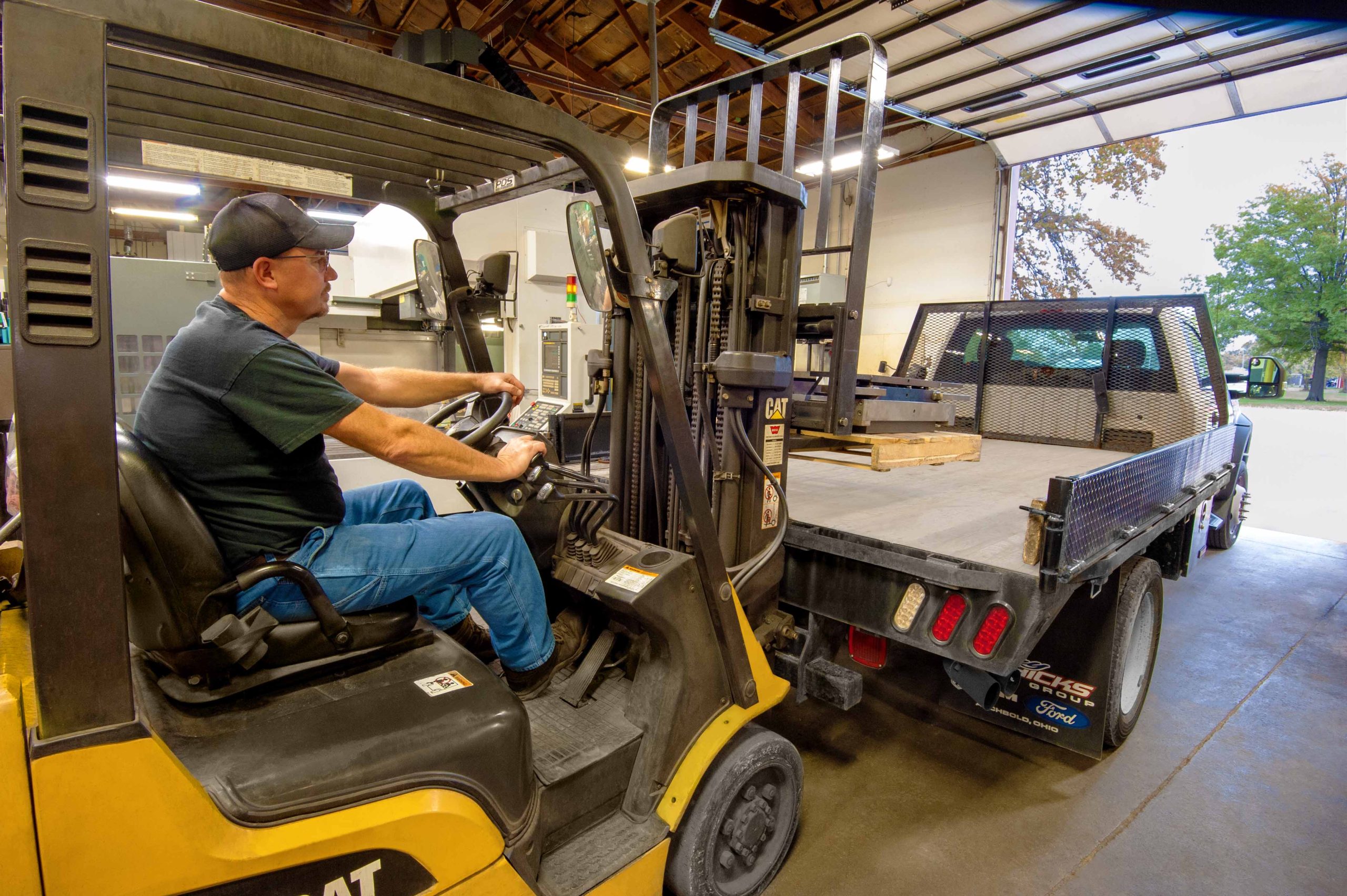
Repair/Replace Services
We find the challenges of repairing old tools or equipment a specialty of ours. Often, the parts needed to get equipment up and running again can’t be found. No problem for DTM. We have the knowledge and experience to reverse engineer the problem. Machine the parts, install and get your equipment up and running again.
Mold repair
Rubber molds can be critical components in the manufacturing process, but they can wear out or become damaged over time due to regular use or operator errors. At DTM, we offer comprehensive rubber mold repair services to restore your molds to their original condition—or even better.
Our mold-making experts specialize in identifying and addressing common issues such as worn cavity walls, damaged interlocks, or misaligned mold components. By refurbishing these critical elements, we help extend the life of your molds and tooling, ensuring consistent and high- quality production.
Engineering and design
Each project starts in the engineering and design phase. Whether you’re working from a completed design or just have a simple sketch, we ensure that your precision parts or tooling components are thoughtfully engineered to meet your needs and budget.
Our skilled engineers use the latest CAD/CAM software to create detailed designs and programming for simple to complex multi-axis parts. Our quality control process starts at the design phase, ensuring components are engineered to the highest standards, and saving you money over the life of the project.
Common issues requiring injection mold repair
The most common issues we encounter during injection mold repairs include:
●Wearable components
Over time, components like dowel pins, springs, and locators wear out and need to be replaced. We specialize in replacing these parts to keep your molds functioning properly.
● Operator errors
Operator errors, such as leaving debris or tools in the mold or misplacing metal inserts, can cause significant mold damage. We can repair these issues, restoring the tooling to its optimal condition.
● Abrasive wear
Rubber is abrasive when injected into steel molds, leading to wear and tear over time. We refurbish these molds by requalifying parting
lines, welding up and re-machining damaged areas, and deepening cavities as needed. This type of tool and die maintenance is critical to the longevity of the tooling.
Automation repair
Automation equipment is key to maintaining productivity, but like any machinery, it can experience wear and tear over time. At DTM, we offer comprehensive automation repair services for when regular maintenance just won’t cut it. We focus on replacing or refurbishing wearable components essential to your automated systems’ smooth operation.
From worn-out gears and bearings to damaged sensors and actuators, our team has the expertise to restore your automation equipment to full functionality..
Engineering and design
Each project starts in the engineering and design phase. Whether you’re working from a completed design or just have a simple sketch, we ensure that your precision parts or tooling components are thoughtfully engineered to meet your needs and budget.
Our skilled engineers use the latest CAD/CAM software to create detailed designs and programming for simple to complex multi-axis parts. Our quality control process starts at the design phase, ensuring components are engineered to the highest standards, and saving you money over the life of the project.
Addressing common automation repair issues
Our automation repair services are designed to address the most common issues that arise with automated systems:
●Wearable components
Over time, components like dowel pins, springs, and locators wear out and need to be replaced. We specialize in replacing these parts to keep your molds functioning properly.
● Operator errors
Operator errors, such as leaving debris or tools in the mold or misplacing metal inserts, can cause significant mold damage. We can repair these issues, restoring the tooling to its optimal condition.
● Abrasive wear
Rubber is abrasive when injected into steel molds, leading to wear and tear over time. We refurbish these molds by requalifying parting
lines, welding up and re-machining damaged areas, and deepening cavities as needed. This type of tool and die maintenance is critical to the longevity of the tooling.
Reverse engineering tools and parts
When parts or tools are no longer available, or when you need to improve upon existing designs, reverse engineering is the solution. At DTM, our reverse engineering tools and processes allow us to accurately measure, test, and replicate parts and metal forms, ensuring they meet or exceed the original
Whether you’re looking to restore a worn-out component or improve its performance, our reverse engineering capabilities provide you with the exact parts you need.
Engineering and design
Each project starts in the engineering and design phase. Whether you’re working from a completed design or just have a simple sketch, we ensure that your precision parts or tooling components are thoughtfully engineered to meet your needs and budget.
Our skilled engineers use the latest CAD/CAM software to create detailed designs and programming for simple to complex multi-axis parts. Our quality control process starts at the design phase, ensuring components are engineered to the highest standards, and saving you money over the life of the project.
The reverse engineering process
1. Assessment
We begin by carefully measuring and testing the part to understand its design and functionality. This step is critical in ensuring that the replacement part matches the original or is improved upon as needed.2. Engineering
3. Machining
Once the design is finalized, we machine the part with precision, ensuring that it fits seamlessly into your equipment and performs reliably.The DTM repair and replacement process: Confidence from concept to completion
At DTM, our repair and replacement process is designed to ensure that every part we restore or replace meets the highest standards of quality and performance. Here’s how we approach each project:
Engineering and design
Each project starts in the engineering and design phase. Whether you’re working from a completed design or just have a simple sketch, we ensure that your precision parts or tooling components are thoughtfully engineered to meet your needs and budget.
Our skilled engineers use the latest CAD/CAM software to create detailed designs and programming for simple to complex multi-axis parts. Our quality control process starts at the design phase, ensuring components are engineered to the highest standards, and saving you money over the life of the project.
1. Initial evaluation
We begin by evaluating the part or mold that needs repair or replacement. This may involve a site visit to assess the equipment on-site or shipping the part to our facility for detailed inspection.
2. Client consultation
After the evaluation, we discuss our findings with the client and recommend the best course of action—whether to repair or replace the part. This decision is driven by factors such as cost, the integrity of the component, and the client’s production needs.
3. Reverse engineering (if necessary)
After the evaluation, we discuss our findings with the client and recommend the best course of action—whether to repair or replace the part. This decision is driven by factors such as cost, the integrity of the component, and the client’s production needs.
4. Repair or replacement
Based on the agreed-upon plan, we either repair the existing part or machine a new one from scratch. Each skilled machinist at DTM ensures that every component is crafted with precision and care.
5. Final testing and installation
Once the repair or replacement is complete, we conduct thorough testing to ensure that the part meets all required specifications. If needed, we also install the part to ensure proper fit and function.
Why choose DTM for your tool and die repair needs?
When you choose DTM for your tool and die repair needs, you’re partnering with a team that is committed to delivering reliable, high-quality solutions. Here’s why DTM is the right choice for your next repair project:
Engineering and design
Each project starts in the engineering and design phase. Whether you’re working from a completed design or just have a simple sketch, we ensure that your precision parts or tooling components are thoughtfully engineered to meet your needs and budget.
Our skilled engineers use the latest CAD/CAM software to create detailed designs and programming for simple to complex multi-axis parts. Our quality control process starts at the design phase, ensuring components are engineered to the highest standards, and saving you money over the life of the project.
Expertise
Once the repair or replacement is complete, we conduct thorough testing to ensure that the part meets all required specifications. If needed, we also nstall the part to ensure proper fit and function.
Precision
Our commitment to precision ensures that every part we repair or replace meets the highest standards of quality and durability.
Customer focus
We work closely with you at every stage of the project, ensuring that your needs are met and that you’re satisfied with the final result.
Quick turnaround
We work closely with you at every stage of the project, ensuring that your needs are met and that you’re satisfied with the final result.